Latest from Training
Sponsored
For anyone desiring a college degree, the price can be daunting in any field.
“The cognitive competencies that are in high demand in the workforce are generally associated with higher levels of education,” notes a report from the Georgetown University Center on Education and the Workforce (CEW). “Today, two out of three jobs require postsecondary education and training, while three out of four jobs in the 1970s required a high school diploma or less. Yet while young people today need more education than ever to compete in the labor market, a college education is more expensive than in the past.”
The 2021 report, “If Not Now, When? The Urgent Need for an All-One-System Approach to Youth Policy,” illustrates that between 1980 and 2020, college costs rose 169%.
“The costs of higher education have risen rapidly over the past few decades, making cost a barrier for many young people who wish to pursue a degree or credential,” the report says. “It used to be possible to work one’s way through college; today, college costs are generally too high—and young people’s wages too low—for that to be feasible. Consequently, more students have to take on larger amounts of debt to get a college degree.”
Work experience is “crucial for young adults, especially those who cannot access or complete postsecondary education,” the report adds. Working after-school or summer jobs allows them “learn new skills and accumulate human capital so they can qualify for decent jobs that pay more than subsistence wages.” However, over the last two decades, youth employment has fallen.
The CEW report explains that the three recessions since 2000—the dot.com bust, the Great Recession and the COVID-19 pandemic—hit younger workers hard. Many find jobs in fast-food restaurants and personal service positions (barbers/hairstylists, child care workers, fitness trainers, animal care workers, recreation workers, etc.). “These occupations provide basic skills but not the higher-level general and technical skills that facilitate movement into good entry-level jobs on promising career pathways,” it notes.
The Skilled Labor Dilemma
Whether you call it trade school, vocational school or career and technical education (CTE), these learning institutions can teach young people the skills and training they need to enter a career with financial stability, such as plumbing, HVACR or electrical. These jobs are fairly recession-proof and cannot be outsourced overseas.
The market size of U.S. trade and technical schools is $15.1 billion in 2022, notes an IBIS World market report. And a Bloomberg article notes that more young people are entering apprenticeship programs in many industries.
“U.S. companies are increasingly tapping high school students for skilled jobs,” the August 2022 article notes. “As a result, apprenticeships are seeing a renaissance after failing to gain a foothold over the past few decades. About 214,000 people aged 16 to 24 were in apprenticeships in 2022, more than double the amount a decade ago, according to July data from the U.S. Department of Labor.”
Bloomberg adds that it’s “part of a national rethink by employers scrambling to fill about 10.7 million vacancies by developing their own talent pipelines.”
Regarding trade careers in construction, plumbing and HVACR are some of the highest-paying trades today. Candidates can obtain a two-year associate’s degree or certification, but many go directly into four- or five-year apprenticeship programs.
The plumbing and heating industries have long experienced the struggle to replace those workers who retire or who, because of job loss during the Great Recession or job dissatisfaction, left for work in other industries,
“Everyone is so focused on college, college, college that the apprenticeship programs have fallen by the wayside as much as the government is trying to push them,” notes Brian Keating, director of the United Service Workers Union (USWU) Joint Apprenticeship Training Fund (JATF). “Many younger people don't even seem to know they exist, nor do their guidance counselors, who are steering them in a particular direction, which is troubling.”
On-the-Job Learning
The “joint” aspect of the apprentice program illustrates the partnership between the JATF, which provides the technical education, and the signatory contractors, who offer on-the-job “learning.”
“We don't call it on-the-job training anymore because what we're teaching here, we want it to be expounded upon at the jobsite, so now you’re teaching it out in the field,” Keating explains. “So, it's on-the-job learning combined with classroom-related instructions. It allows apprentices to apply the knowledge they acquire in the classroom to their work during the day. They don’t forget.”
Keating has spent most of his 45-year career in the HVAC industry and headed up the USWU JATF for the last 12 years. He is an OSHA-approved trainer for occupational safety and health, also approved by the New York City Department of Buildings. Keating also is a master trainer for the National Center for Construction, Education and Research.
One of Keating’s main goals for the school is to attract more young people into the construction specialty trades.
“I've spoken at some women’s groups, and there's such an opportunity here for them,” he says. “They can make a living wage, with full medical, dental, and life insurance, all paid for by the employer. Say you're making $2 an hour; that $2 is all yours. You don't have to contribute 25 cents to your medical, 10 cents to this, and 20 cents to that.”
Keating notes that some colleges promise young people “ridiculous” six-figure salaries once they obtain a college degree. “You're not going to get that salary right out of college because you have no experience,” he explains. “How can I possibly pay you that kind of money? However, with an apprenticeship, you're not only getting a formal education at a college level, but you're also getting the experience because you're working full time.”
Before prospective apprentices commit to the JATF, Keating brings them in to discuss the program. He encourages young people to include their parents and explains the curriculum. Keating demonstrates the tools and projects they may work on.
“I want them to have a good idea of what the job entails,” he says. “And I want them to research it. If you want to be a sheet metal worker, go online and research sheet metal work and what's involved in it. Is it something you'd be comfortable doing and making a career out of?”
The US Bureau of Labor Statistics (BLS) reports that the median annual salary of plumbers, pipefitters and steamfitters was $59,880 in early 2021. The lowest 10% earned less than $36,700, and the highest 10% earned more than $99,920.
Of course, plumbing wages depend on years of experience and whether you are an apprentice, journeyman or master plumber, union or nonunion. The BLS figures do not make that distinction.
Safety First
Keating explains that apprentices begin with the four-month core program, introducing them to hand tools, power tools, blueprints and construction math. First, however, apprentices must attend a 30-hour OSHA course.
“We want to make sure these new individuals going out into the field will work safely on a ladder or using a hand or a power tool so we can minimize or eliminate any injuries happening on the jobsite,” Keating says.
When apprentices return after the holidays in January, they start Level 1 courses in their particular disciplines. The piping programs—fire sprinkler, steamfitting, plumbing and HVAC—are all five-year programs. They go to class for four hours two nights a week and work full-time during the day.
“We don't bring anyone into our program unless we have a job for them,” Keating states.
The USWU JATF sheet metal program is a four-year program, which includes a 100-hour safety program divided into 25-hour segments over those four years. “I think it comes to around 175 hours of safety training throughout their apprenticeship,” Keating notes. “So they're well-versed in safety.”
He adds: “I'm pretty big on safety. Life-changing, on-the-job accidents can affect an entire family. Maybe they must deal with a family member’s disability, or what was once a two-income household is now only one. So, their safety is very important. We want to ensure that apprentices recognize hazards and know how to deal with them appropriately.”
A Career, Not a Job
Keating attends high-school job fairs, but he prefers one-on-one time with guidance counselors and teachers to educate them on what the USWU JATF is about and what resources are available to them and students.
He is also trying to recruit more women into the trades. Keating works with the global organization Dress for Success at its Long Island location. Its mission is to “empower women to achieve economic independence by providing a network of support, professional attire and the development tools to help women thrive in work and life.”
Keating explains: “If you look at any study throughout the country, thousands and thousands of construction jobs are available, looking to be filled. I’ve been trying to get the young women at Dress for Success to look at our apprenticeship program. It's not all grunt work, and it's not all terrible: it's education, money and benefit packages available to them and, if they are single moms, their children. The work is here and a great opportunity for them to build a career.”
He also battles with plumber stereotypes. “It's a different profession than it used to be many years ago,” Keating remarks. “We're your next-door neighbor. We're the same person you see at church, the soccer field or the grocery store.
“When you say plumbing, they think of the plumber under your kitchen sink. We're talking about putting office buildings up with plumbing running up 42 floors. If not sized and installed correctly, those systems you put in aren't going to be working properly. These construction trades involve many technical aspects you must be properly trained on.”
Keating acknowledges that the construction specialty trades aren’t for everyone, but the union isn’t looking for bodies to fill spaces.
“We're not looking for people who want jobs; we're looking for people who want careers,” he explains. “This is a viable and lucrative career path. This isn't like getting a job at a big-box store and making a career there. Many people do and that's great, but we're looking for career-minded people because of what we offer.”
Kelly Faloon is a contributing writer to CONTRACTOR Magazine and owner of Faloon Editorial Services. The former editor of Plumbing & Mechanical magazine, she has nearly 35 years of experience in B2B publishing, with 25 of those years writing about the plumbing, heating, cooling and piping industry. Faloon is a journalism graduate of Michigan State University. You can reach her at [email protected].
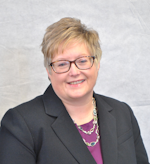
Kelly L. Faloon | Freelance Writer/Editor
Kelly L. Faloon is a contributing editor and writer to Contractor, Contracting Business magazine and HPAC Engineering and principal of Faloon Editorial Services. The former editor of Plumbing & Mechanical magazine, Faloon has more than 26 years of experience in the plumbing and heating industry and more than 35 years in B2B publishing. She started a freelance writing and editing business in 2017, where she has a varied clientele.
Faloon spent 3 1/2 years at Supply House Times before joining the Plumbing & Mechanical staff in 2001. Previously, she spent nearly 10 years at CCH/Wolters Kluwer, a publishing firm specializing in business and tax law, where she wore many hats — proofreader, writer/editor for a daily tax publication, and Internal Revenue Code editor.
A native of Michigan’s northern Lower Peninsula, Faloon is a journalism graduate of Michigan State University. You can reach her at [email protected].