3D Modeling: Save Money, Reduce Risk, Increase Productivity
The construction industry has a love-hate relationship with technology. Some are wary of any new software/hardware the boss brings back from a convention or trade show. In fact, much of this software and equipment help automate certain processes to reduce errors, increase productivity and save money. All good things, right?
3D modeling is a family of technologies that collect pre-construction, construction and post-construction data into one repository. Conditions can be easily changed, and the entire construction team can view those changes in real time.
However, 3D modeling software is still not 100% adopted by the industry, including mechanical/electrical/plumbing (MEP) contractors. We spoke with Matt Curry, head of product at Avvir, about this 3D adoption problem, and uses for artificial intelligence (AI) and reality capture in today’s construction landscape.
CONTRACTOR: First, let’s take a broad view of 3D modeling software use in the construction industry. Do you still see a reluctance for construction professionals to use this technology?
We see that BIM becomes more common as project complexity increases. This also bears out in the numbers, according to a 2022 American Institute of Architects survey—architects use BIM on 100% of large-sized projects (http://bit.ly/3yXXm4G).
CTR: Going to the subcontractor level, how comfortable are MEP contractors—specifically plumbing and mechanical contractors—using such software on their projects?
MC: For large construction projects, MEP contractors are generally comfortable using BIM on their projects. It’s a capability many MEP contractors have built up in-house to remain competitive when bidding. This comfort shows up in the overall industry adoption rates.
CTR: What about the adoption of AI and reality capture technology in the construction industry?
MC: Let’s break this down:
1. AI
• AI powers robots such as drones and Boston Dynamics’ Spot (http://bit.ly/3FHANoV) to navigate the jobsite, but this is often opaque to trades.
• Explicit AI use cases where the contractor is aware of the results are much lower than 3D modeling; it often requires a form of reality capture to already exist on the project.
• During design phases, MEP trades can use general AI/algorithms to automate the drawing and calculating of pipe runs and ductwork
2. Reality capture
• Adoption of 360-degree or 2D photos, a form of reality capture, is much higher than 3D modeling. Almost all projects use some form of photo documentation, as it’s a typical contract requirement.
• Drones have gained adoption in the last four to five years as prices have come down and the software and skill required to run them significantly increased. These technologies help automate reality capture.
• Point clouds from LiDAR, another form of reality capture, are less adopted: about 48% of projects use them, according to the 2022 Builtworlds Preconstruction survey (http://bit.ly/3JXkR4f).
Avvir is on the cutting edge of this adoption as we use AI to analyze photos and point clouds against BIM to provide automated schedule tracking, cost and earned value analysis, installation issue detection and updated as-built BIM.
CTR: How can the industry convince reluctant MEP contractors to take a chance on this technology?
Beyond proving it, the industry can help MEP contractors adopt 3D modeling by making the process easier and quicker. Two of the biggest adoption barriers are the skills required to do the modeling work and the upfront time required to get it done. Some startups are trying to tackle this problem but don’t have widespread adoption.
CTR: With high construction costs, how does 3D modeling technology save MEP contractors money?
MC: 3D modeling can help MEP contractors save money during the design and construction phases of the project.
To elaborate, in the planning phase, BIM modeling and federation (the process by which all subs models are “collected” into a single source of truth) can help ensure MEP designs have fewer-to-no conflicts with other trades, reducing the amount of field coordination and possible rework. This process reduces the back-and-forth required to coordinate complex work across multiple trades.
During construction, modeling design changes in the BIM can reduce the amount of coordination around change orders or other field coordination issues. Many projects keep their BIM current when fieldwork diverges from the design plan. Coordinating around an up-to-date BIM makes coordination quick, easy and effective, allowing trades to focus on actually building and staying on schedule.
CTR: Productivity issues are always a concern on construction jobsites. Can these high-tech software products help keep workers efficient and accurate?
MC: BIM by itself can improve productivity by making it easier for trades on-site to be efficient and accurate. It does this by helping improve the planning and coordination processes. Think of the adage, “Measure twice, cut once.” BIM enables you to build the project virtually to uncover mistakes before you get into actual construction.
Real productivity comes when you combine BIM with point clouds from a LiDAR scanner. This analysis can improve productivity by catching mistakes before they become too costly (i.e., quality control). To find mistakes, a project team scans an area of their project, loads the point cloud into software on a computer, and analyzes the point cloud to detect issues.
A skilled virtual design and construction team, or users of Avvir’s software, can identify when walls aren’t plumb, concrete isn’t flat or if contractors made installation mistakes—without having to inspect the site in detail. Automating this process yields massive efficiency gains.
CTR: Can this technology identify safety issues?
During design, you can use BIM to identify potential safety issues by finding code violations or catching poor planning. While certain parts of the permitting process are out of your control, BIM can automate a baseline adherence to code. This automation drastically reduces the permitting review process.
For example, a product called ComCheck automates and speeds up the process of confirming energy code compliance checking for commercial buildings.
BIM allows for more careful, detailed planning and coordination before a project breaks ground, which leads to improved on-site safety.
Similarly, during construction, you can compare the BIM to other forms of reality capture (e.g., 360-degree photos or LiDAR) to remotely monitor your jobsite’s progress. Remote monitoring reduces the number of people on-site, which reduces the possibility of safety issues.
Beyond this, remote monitoring often results in weekly documentation and visual issue identification used to encourage and manage safe, clean working conditions.
CTR: What about risk analysis?
MC: BIM by itself can reduce the risk of schedule delays and project overruns by improving planning. However, to truly manage risk with BIM, it needs to be connected to a form of reality capture with advanced analysis on top of the data.
Avvir helps with this by connecting your BIM and reality capture into a single point for insights and context. It connects pre-construction design data (schedule, work breakdown structure, quantity takeoff, BIM) to construction data (360-degree photos and videos, LiDAR point clouds).
Combined with advanced AI on top of this data, Avvir gives project teams control and insights with automated schedule tracking, cost and earned value analysis, installation issue detection and an updated BIM with as-built conditions.
CTR: What are the top three issues most overlooked on construction projects? How can 3D technology help resolve them?
Second, data silos. When data is created and used, it often sits in a silo. You do one task (e.g., status your BIM manually to determine what is built and not built, using BIM as the canonical truth for design to calculate building progress), but follow-on tasks are frequently done independently. For example, it is common for a project to status its BIM but still use the super’s estimate for calculating progress when updating schedules.
Third, data mistakes. Not only is there too much data living separate from other data but there is a human element to enter, synthesize and make sense of the data. Humans are great problem-solvers, but anything done manually introduces potential human-created errors.
3D modeling can reduce these problems by centralizing all data into the model, creating a canonical, always up-to-date repository of project information. This requires time, dedication and skill of the GC and the trades.
Avvir simplifies connecting, synthesizing and acting on this firehouse of data with an accessible, friendly user interface that encourages total team interaction.
CTR: What advice would you give MEP contractors considering adopting this type of technology?
MC: I think the most important advice I can give is to accept that you will make mistakes at first. 3D modeling is a skill that requires practice to become competent. It’s easy to try it once, make a mistake, and give up on the technology and process. It’ll take a few tries to fully master the skill and integrate the modeling into your progress.
Luckily, many resources are available to get started and the technology is more accessible than ever. There are good, publicly available “how to” guides and step-by-step videos online for a motivated subcontractor to increase skills and prepare for the future. The more sophisticated GCs are eager to partner with advanced MEP subcontractors and will eagerly collaborate on 3D modeling.
About the Author
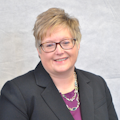
Kelly L. Faloon
Freelance Writer/Editor
Kelly L. Faloon is a contributing editor and writer to Contractor, Contracting Business magazine and HPAC Engineering and principal of Faloon Editorial Services. The former editor of Plumbing & Mechanical magazine, Faloon has more than 26 years of experience in the plumbing and heating industry and more than 35 years in B2B publishing. She started a freelance writing and editing business in 2017, where she has a varied clientele.
Faloon spent 3 1/2 years at Supply House Times before joining the Plumbing & Mechanical staff in 2001. Previously, she spent nearly 10 years at CCH/Wolters Kluwer, a publishing firm specializing in business and tax law, where she wore many hats — proofreader, writer/editor for a daily tax publication, and Internal Revenue Code editor.
A native of Michigan’s northern Lower Peninsula, Faloon is a journalism graduate of Michigan State University. You can reach her at [email protected].