Latest from Radiant
eBook: Nelson Mechanical Stories - Volume 1
Sponsored
The Cleveland Clinic and Case Western Reserve University will open its Health Care Education facility, built on 11 acres, in summer 2019. The centerpiece four-story, 485,000-sq.-ft. Sheila and Eric Samson Pavilion will house classrooms and labs for 2,200 medical, nursing, dental and physician assistant students.
Designed by London's Foster + Partners architects, the Samson Pavilion will feature a 27,000-sq.-ft. central atrium; admissions and academic learning environments on the first floor; and an innovation laboratory, where students and faculty can develop and test new technologies and pilot their use in health-care education — such as Microsoft’s augmented reality device, HoloLens, for lessons in subjects such as anatomy.
“Health care increasingly is a team sport,” says Toby Cosgrove, CEO and president of Cleveland Clinic. “The students who graduate from these programs will be uniquely prepared to participate and lead in this new era.”
For the Samson Pavilion’s atrium, the building’s owners chose a radiant floor heating and cooling system to be installed under the granite floor to provide the best comfort for students and faculty.
“From an energy standpoint, it’s a much more efficient way to heat the air rather than blowing air around,” says Dan Kronenfeld, project manager for Walton Hills, Ohio-based mechanical contractor Smith and Oby Co. “Keeping the floor warm and the heat near the floor is going to be extremely efficient in this application.”
The project engineers specified Uponor’s Radiant Rollout Mats to expedite the main level’s radiant installation. “I believe the radiant system was specified because there wasn't a way to get enough air flow into that area,” Kronenfeld notes. “The engineers’ modeling didn't allow them to keep the heat in the zone where they needed it any other way.”
The Smith and Oby crew installed 86 mats of 55,860 lineal feet of PEX tubing throughout the atrium. The mats consist of a custom-designed, prefabricated network of Wirsbo hePEX barrier tubing connected with ProPEX1 engineered polymer fittings, which are safe for burial in the slab. They use 80 percent fewer manifold ports due to small piping networks and 40 percent fewer wire ties or staples to minimize strain on workers' bodies.
“The biggest advantage for us was two-fold,” Kronenfeld says. “First, the labor savings. When you run pipe in loops, the guys spend a lot of time on their knees moving back and forth, stapling PEX to rebar or the subfloor. The mat reduces labor — the crew rolls out each numbered mat in its location, then attaches it to the floor. The hardest part is taking the memory out of it because it wants to roll back up.”
The second advantage is saving time in the schedule, he adds. Smith and Oby had a narrow window to install the PEX pipe as the slab was four layers — the initial structural pour, insulation board, another concrete pour, the Rollout Mat, then the last concrete pour before adding the grout layer and the granite.
“If we had laid that out by hand without the mats, it might have taken about four months — six to eight guys a month per area,” he notes. “With the mats, we did the atrium in a little more than a month. The schedule savings was enormous. Uponor was prefabricating the mats while the facility was being built.”
The system also includes radiant cooling; the mats had 5/8-in. and 3/4-in. PEX pipe turned on 6-in. centers. That size tubing can be difficult to bend without kinking the hose, so the Smith and Oby crew avoided the problem with the radiant mats. “When you have 6-in. centers like they wanted with the larger pipe, many times you have to bubble the ends and bring it back,” Kronenfeld says. “They lay over the top of each other and it's much more difficult. The mats were pre-manufactured with the correct centers.”
“The biggest challenge on the project was alleviating the concerns of the facilities staff and the owners about having joints under the floor,” he adds. “They see those joints as a point of failure. If a leak occurred, a portion of the granite floor would need to be removed to make the repair.”
Representatives from Uponor arrived on the jobsite and explained how the joints go together, as well as the failure rates, which put to rest the concerns of the engineers, facilities management and owners’ representatives.
Snowmelt, too
The HEC also will have three areas of snowmelt for the safety of students, faculty and visitors.
“We completed area one on the east side of the building, which is the largest area,” Kronenfeld explains. “That was fed off of one of the risers going up to the central utility plant, which has a water-to-glycol heat pump for the system. It has four individual zone boxes feeding off the mains to feed different manifolds. A second run goes down to the west side and then also feeds the north side. Those two areas have three more zone boxes.”
As of this writing, about half of the snowmelt is installed, with the turnover to the owners set at Dec. 15 of this year.
In addition to the radiant floor heating and cooling system, Smith and Oby installed 700 chilled beams on the fourth floor (for radiant cooling), 300 VAV units from the third floor down, a chiller plant with three chillers, a boiler plant with three boilers and 16 air-handling units (including four dedicated outdoor air systems). The DOAS units provide outside air to the standard air handlers and the chilled beam system. A separate cooling system — the process chilled water system — feeds the IT and AV closets for the building.
The HEC project is one of the largest for Smith and Oby at almost $40 million. While the building’s heating and cooling systems are not complex, it’s the size of the building that stands out. The site is about a city block and the HEC building takes up about one-third of it.
“The prefabrication was the best part of it for us — we were able to maintain the very tight schedule window without men tripping over each other,” Kronenfeld says.
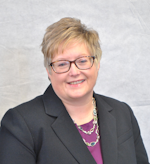
Kelly L. Faloon | Freelance Writer/Editor
Kelly L. Faloon is a contributing editor and writer to Contractor, Contracting Business magazine and HPAC Engineering and principal of Faloon Editorial Services. The former editor of Plumbing & Mechanical magazine, Faloon has more than 26 years of experience in the plumbing and heating industry and more than 35 years in B2B publishing. She started a freelance writing and editing business in 2017, where she has a varied clientele.
Faloon spent 3 1/2 years at Supply House Times before joining the Plumbing & Mechanical staff in 2001. Previously, she spent nearly 10 years at CCH/Wolters Kluwer, a publishing firm specializing in business and tax law, where she wore many hats — proofreader, writer/editor for a daily tax publication, and Internal Revenue Code editor.
A native of Michigan’s northern Lower Peninsula, Faloon is a journalism graduate of Michigan State University. You can reach her at [email protected].