Latest from Piping
Sponsored
New Technical Document: Applying Spray Foam Insulation in and Around Plastic Pipes
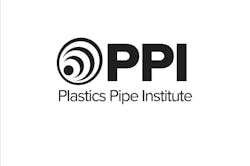
IRVING, TX — A new technical document that addresses techniques for the safe and proper use of spray polyurethane foam insulation on and around plastic pressure pipe materials has been published by the Plastics Pipe Institute, Inc. (PPI) with input from the Spray Polyurethane Foam Alliance (SPFA).
Prepared by PPI’s Building & Construction Division, PPI TN-69 Recommendations when Applying Spray Polyurethane Foam Insulation on and around Plastic Pressure Pipes & Fittings discusses the proper application of spray polyurethane foam insulation to avoid damage due to heat generated by the foam. Pipe and fitting materials include CPVC, PEX, PEX/AL/PEX, PE-RT, PP-R, PP-RCT, PSU, PPS, PPSU, and PVDF.
Plastic pressure pipes and fittings are commonly used in applications such as hot- and cold-water plumbing, fire protection, and hydronic heating and cooling systems, including radiant distribution systems. In certain instances, pipes and fittings are installed inside areas that must be insulated, such as within a ceiling or wall cavity. In other installations, the pipes and fittings themselves must be insulated to reduce the transfer of heat through the pipe wall.
Spray Polyurethane Foam
According to the SPFA, Spray Polyurethane Foam, or SPF, is a high-performance insulation material commonly used in homes and buildings of all types, and has been used as insulation for decades.
“The spray polyurethane foam curing reaction is exothermic,” explained Richard Duncan, Ph.D., P.E., executive director of SPFA, “which means that heat is generated during the foam reaction. The heat of reaction is highly dependent on the SPF formulation and is also based upon the overall intended application or lift (i.e., layer) thickness installed. Peak temperature within the layer of foam typically occurs within 5 to 15 minutes of application, followed by gradual cooling.”
According to SPFA documents, the chemical reaction that takes place during the application and curing of SPF will generate exothermic temperatures above the 120°F - 130°F setpoint temperatures of the proportioner and hoses. Peak temperatures at the mid-thickness of a pass can exceed 200°F for several minutes and reach peak temperatures 250°F - 275°F for a minute or two, especially for closed-cell SPF, when applied at the maximum pass thickness.
“Plastic pipes and fittings in both residential and commercial plumbing, residential fire protection, and most hydronic applications are typically required to have pressure ratings at 180°F (82°C) operating temperature,” explained Lance MacNevin, P. Eng., director of engineering for PPI's Building & Construction Division.
MacNevin continued, “The plastic pipes and fittings referenced in PPI TN-69 will withstand short-term exposure to temperatures above 180°F. However, exposure to temperatures above the rated operating temperature of each material, which may occur if pipes are encased in a thick pass of closed-cell SPF, are likely to have negative effects on these materials, potentially leading to premature failure. It is important that SPF insulation is installed correctly to prevent overheating of pipes and fittings.”
Access the full content of PPI TN-69 at https://plasticpipe.org/common/Uploaded%20files/Technical/TN-69/PPI%20TN-69.pdf.
Additional information and data about pressure pipe materials used for plumbing and mechanical systems are available from the PPI Building & Construction Division at www.plasticpipe.org/buildingconstruction