PHCP Insights from the Longshoremen’s Association Port Strike
On Oct. 1, about 45,000 East and Gulf Coast dockworkers at 36 ports went on strike over wages, automation, healthcare and other issues. Covering ports from Maine to Texas, members of the International Longshoremen’s Association (ILA) walked out as their contract with the United States Maritime Alliance expired, reported the Associated Press. “Workers began picketing at the Port of Philadelphia shortly after midnight, … even though progress was reported in talks on [the previous day]. The strike … is the first by the union since 1977.”
Construction Dive (https://bit.ly/40g3Cnt, https://on.wsj.com/4fiIq4v) notes that “the impacted ports are some of the main points of entry for construction materials, heavy machinery, food, vehicles and chemicals. … Exports of oil and liquefied natural gas at Gulf Coast ports will likely be unaffected because the ILA has little or no involvement in those operations.”
National Association of Wholesaler-Distributors President and CEO Eric Hoplin stated: “The East and Gulf Coast port strike is putting our economy and national security at risk. This strike isn’t just about disrupting a few shipments; it’s about stopping the supply chain and bringing the flow of critical goods to a standstill.
“The damage could reach $5 billion a day, with small and mid-sized businesses at risk due to missed deliveries and empty shelves. … This is not just about pay or shipping delays—it’s about our global competitiveness. The ILA’s demands to ban automation in ports will cripple our ability to compete internationally, while ports in Europe and Asia embrace automation and technology to stay ahead.”
National Association of Manufacturers President and CEO Jay Timmons said: “There will be dire economic consequences on the manufacturing supply chain if a strike occurs for even a brief period. [Our] estimates show a strike at the East and Gulf Coast ports would jeopardize $2.1 billion in trade daily, and the total economic damage could reduce GDP by as much as $5 billion per day.”
The American Supply Association’s (ASA) September economic report (https://bit.ly/3BSyZu2) noted: “Estimates show that a work stoppage extending more than a week could take more than [three to five] weeks to unravel. If the strike were to go more than [three] weeks, it might take until January of 2026 to get backlogs cleared. In the meantime, inventories will be depleted in the near term as shipping stalls and shipping costs will rise in the months to come as containers and ships get moderately stranded awaiting docking.”
However, it appeared that a long, drawn-out strike would not occur.
Surprisingly, a joint statement made Oct. 3 said a tentative wage agreement had been reached, and the parties agreed to extend the six-year contract until Jan. 15, 2025. This would allow both sides to negotiate the remaining labor issues. “Postponed” and “on pause” have been used to describe the strike’s status as automation and healthcare issues are discussed. ILA members must still vote on the full agreement before the strike is fully resolved.
Mixed Impact for PHCP Distributors, Manufacturers
ASA surveyed its members before the strike started to determine the impact of the potential supply chain disruption on PHCP distributors and manufacturers—especially after having navigated the COVID-19 pandemic’s extended slowdown (https://bit.ly/4ffupnV).
“We have been following this potential for several months,” one ASA PVF-focused supplier said. “A strike will be a major disruption in the supply chain for many critical items. We have prepared as best we can to maintain raw materials [coming] into the East Coast ports.”
Another member noted: “A dock workers strike would impact our ability to service our customers' needs. Increased lead times in our supply chain could impact critical infrastructure.”
Some suppliers would be all right in the short term, but a long-term strike would cause problems.
One supplier using both coasts said: “We bring our appliances and some plumbing products through the East Coast ports, but the majority is coming through the West Coast ports, so … with our current inventory levels, which we have increased in the prior month, we do not feel it would be a major impact in the near term, 30 [to] 60 days.”
Another noted: “This is a fluid situation; if there is a strike, how long does it last? We have been evaluating inventory levels and putting contingency plans such as rerouting of containers to minimize the impact [on] our business operations.”
“[E]ach day of a strike increases our raw material lead times by 3.5 days. The real risk is not immediate but 90 days later when supply chains are exhausted, and delays have slowed replenishments,” a member explained.
And yet others were less concerned as either their shipments went into West Coast ports or their materials originated from the United States.
• “Minimal at worst, providing there is [no] sympathy strike as we receive inventory through US West Coast ports like Long Beach.”
• “None, unless this lingers until early 2025; then, it might affect a few of our products. We have very few imported items.”
• “We have material on hand that our suppliers have in [a] warehouse near our manufacturing facilities for specific problems like this.”
• “We manufacture in the United States and use Made in the USA sources for supplies and raw materials.”
Alternative Shipping, Sourcing Plans
The talks had been going on for months, giving ASA members time to make contingency plans.
“If we do have a delay in product deliveries, our customer service will provide wholesalers with options for alternative products that are in stock,” one manufacturer said. “We will also shift some products to North America plants in the short term if needed.”
Another noted: “We’re using different ports and points of travel to try and mitigate the issue.”
One member “identified alternative routes for deliveries. That said, we expect significant congestion/delays as others implement similar strategies.”
“We are building [an] inventory of finished goods to lessen the chances that shipments to wholesalers will get delayed,” a manufacturer member noted.
Other comments include:
• “We pivoted rod sourcing to Mexico and on steel pipe, we'll be offering a domestic solution on certain SKUs if we experience stock outages from the supply chain interruptions.”
• “We have been actively rerouting containers to unaffected ports.”
• “We have sufficient inventory of imported materials to last us on average 1.5 to 3 months. Alternatives include offering domestically produced materials, working with competitors and other distributors, and possibly importing very small amounts by air.”
• “We have increased production here, anticipating our competitors having shipping issues.”
• “We have developed new sources and strategies to minimize impact.”
One member lamented the industry’s dependence on imported materials: “What measures can be put into place? Most of the material we sell is either manufactured abroad or some of the components for the goods are manufactured abroad. Our industry is heavily dependent on ports. … Using domestic sources is an option sometimes, but not all items are made here in the US, and the production capacity of the US manufacturers could not support all our industry.”
What’s Next?
Luckily, the three-day strike did not affect hurricane relief efforts. “Despite talk of the strike affecting hurricane recovery efforts, there was almost no impact on the flow of emergency supplies to storm victims,” noted CNN Business (https://cnn.it/3YxOLn4). “All … the ships calling on those ports are foreign-owned vessels coming from overseas ports. Under well-established US maritime law, those ships are not allowed to transport goods from one US port to another.”
However, CNN noted that there is still some cause for concern.
“[The] deal likely is the end of the strike, but it doesn’t close the door on a new strike in the future,” the network reported. “The final language in the full contract … will need to be ratified by the union’s rank-and-file members before it can take effect. Should the members vote against the deal, the strike might start once again. And such a rejection of a tentative labor deal is not unheard of.”
ILA members are wary of automation taking their jobs, but port operators need to invest in the technology to stay competitive.
“A focus on keeping ‘historical job functions’ will inevitably continue to undermine the competitiveness of US East and Gulf Coast ports in a global context,” said CEO of Vespucci Maritime Lars Jensen (https://bit.ly/4eSLqVq).
Founding director of USC Marshall’s Kendrick Global Supply Chain Institute, Nick Vyas, told Supply Chain Dive (https://bit.ly/3NEn9Go): “As US ports—East Coast and West Coast alike—grapple with rising costs and the need for greater efficiency, the push to modernize through automation is inevitable. Yet, this creates a fundamental tension between labor and port operators.
“The outcome of these negotiations may set a precedent for the future of port operations in the US, determining whether labor-intensive jobs will survive in the face of technological advancement.”
According to consultant Gartner (https://gtnr.it/4dYFuZq), Chief Supply Chain Officers can take this opportunity to proactively work on logistics risk management and protect their companies from inevitable supply chain disruptions.
“The latest strike is just another reminder that supply chains must shift from reactive approaches to more sustainable and efficient integration of supply chain risk management, and planning into logistics,” it noted. “With the US port workers’ strike on pause, supply chain leaders can return to boosting their preparedness.”
Kelly Faloon is a contributing writer to CONTRACTOR magazine and principal of Faloon Editorial Services. The former editor of Plumbing & Mechanical magazine, she has more than 35 years of experience in B2B publishing, with 26 of those years writing about the plumbing, heating, cooling and piping industry. Faloon is a journalism graduate of Michigan State University. You can reach her at [email protected].
About the Author
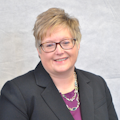
Kelly L. Faloon
Freelance Writer/Editor
Kelly L. Faloon is a contributing editor and writer to Contractor, Contracting Business magazine and HPAC Engineering and principal of Faloon Editorial Services. The former editor of Plumbing & Mechanical magazine, Faloon has more than 26 years of experience in the plumbing and heating industry and more than 35 years in B2B publishing. She started a freelance writing and editing business in 2017, where she has a varied clientele.
Faloon spent 3 1/2 years at Supply House Times before joining the Plumbing & Mechanical staff in 2001. Previously, she spent nearly 10 years at CCH/Wolters Kluwer, a publishing firm specializing in business and tax law, where she wore many hats — proofreader, writer/editor for a daily tax publication, and Internal Revenue Code editor.
A native of Michigan’s northern Lower Peninsula, Faloon is a journalism graduate of Michigan State University. You can reach her at [email protected].